At Abtrex Industries, we specialize in protecting your critical equipment from corrosion and abrasion, as well as providing custom fabrications. In addition to steel, our team has extensive experience in fiberglass fabrication for a wide range of applications.
Fiberglass fabrication has become increasingly popular due to its exceptional durability, lightweight nature, and chemical resistance. FRP (Fiberglass Reinforced Plastic) products are widely used across various industries, including energy, aviation, pharmaceuticals, marine, automotive, sporting goods, and home products. FRP offers outstanding durability for handling chemicals like chlorine, hydrochloric acid, sodium hydroxide, titanium dioxide, sulfuric acid, and bleach.
What is Fiberglass Reinforced Plastic (FRP)?
Fiberglass Reinforced Plastic (FRP) is a composite material made by embedding carrier fibers into a thermosetting resin. The resin strengthens the fibers and facilitates the transfer of shear stresses between them. In our production process, we mainly use thermoset resins:
- Epoxy Vinyl Ester – Ideal for highly corrosive environments due to its resistance to strong acids, bleaches and alkalis. Vinyl ester provides high impact resistance and is particularly effective for laminating. There are various types of epoxy resin, and the material selection depends on the intended use and project requirements.
- Polyester – An economical synthetic resin suitable for general applications, offering a short curing time. It is a reliable choice for chlorine service.
Mixing resin with other materials may bring additional properties and advantages. A blend of polyester or epoxy vinyl ester resin combined with silicon carbide is particularly effective in handling abrasive slurries. The resin provides excellent corrosion resistance, while the silicon carbide effectively addresses wear concerns in your fabrications. The abrasion-resistant barrier can be applied to both new and existing equipment
Fiberglass Types
The resin provides corrosion protection and chemical resistance, but on its own, it lacks the strength needed to maintain the required shape of the equipment. To ensure structural integrity, fiberglass is added in the form of chopped strand mat or woven roving. When combined, the resin and fiberglass provide both the protective qualities, and the strength needed to withstand the demands of the application.
Chopped Strand Mat (CSM) is an excellent solution for corrosion protection. The glass fibers are chopped and embedded in the resin, making it more difficult for corrosive factors to penetrate. The mat is typically combined with polyester or vinyl ester resins. Due to the random orientation of the fibers, CSM can be easily molded into various shapes. It is commonly used for building up construction thickness and for repair work.
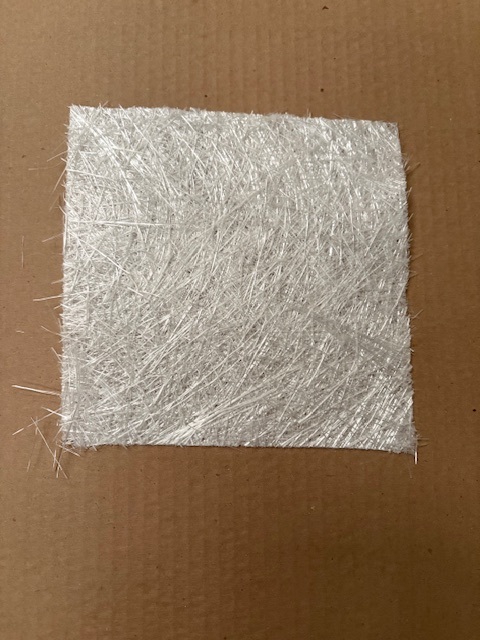
Fiberglass Reinforced Plastic Chopped Strand Mat
Woven Roving is used to produce laminates, reinforcing polyester or epoxy resins. It is known for its high tear strength, low density, excellent thermal resistance, low hygroscopicity, and good electrical insulation properties. The material is non-flammable, chemically inert, and resistant to corrosion, molding, and rotting. Due to its reinforcement properties, woven roving can be combined with chopped strand mat to achieve enhanced strength for larger forms. In certain applications, Fiberglass Reinforced Plastic (FRP) can also be used alongside rubber linings for additional protection of your equipment.
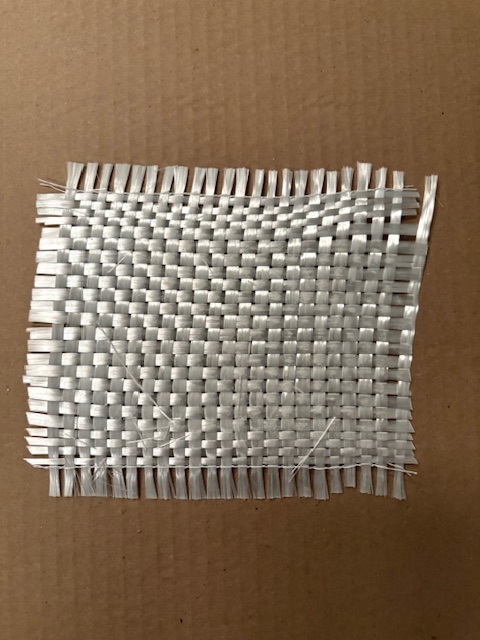
Fiberglass Reinforced Plastic Woven Roving
Nexus Veil is a synthetic surfacing veil used as the first layer in FRP fabrication to create a smooth inner surface. Its excellent resin absorption capability allows the inner layer to consist of 90% resin and only 10% veil, ensuring superior chemical resistance. This composition enhances durability and protection in corrosive environments.
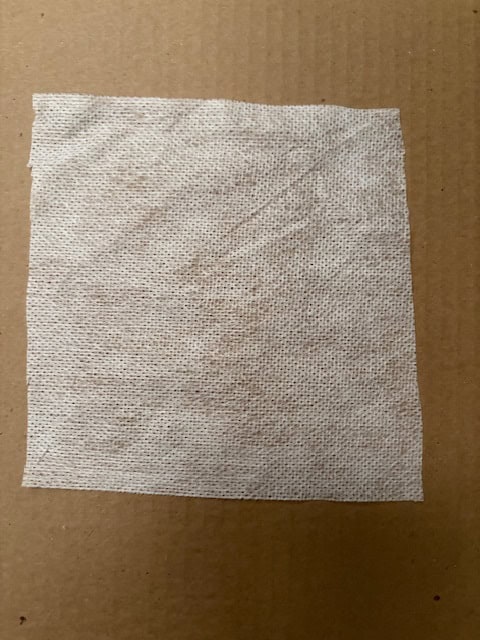
Fiberglass Reinforced Plastic Nexus Veil
“C” Veil used at Abtrex is a glass surfacing veil designed for both outer and inner surfaces, providing excellent corrosion protection, including against dripping exposure. It ensures a smooth final surface with an appealing visual finish. Composed of 90% resin and 10% veil, it provides excellent durability and protection.
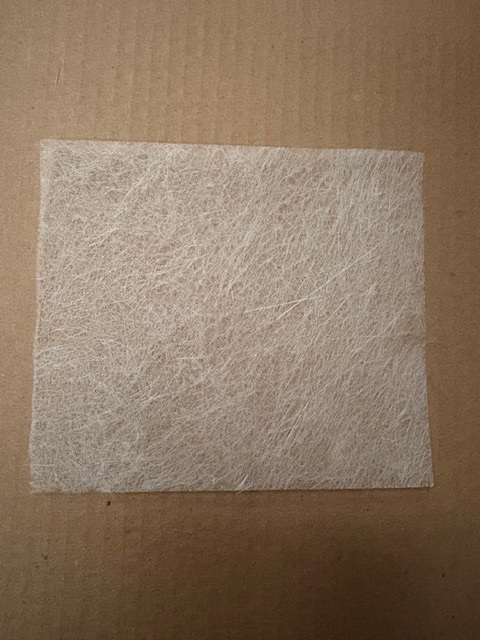
Fiberglass Reinforced Plastic C Veil
The choice of resin, glass type, and their proportions is determined by the specific chemical solution that will pass through the equipment, as each fabrication at Abtrex is customized to meet the unique requirements of every project.
The thickness of the FRP construction will depend on the pressure rating of your equipment, and can be built for pressure ranging from 25 PSI to 150 PSI, and pipe diameter from 2” to 60”.
Abtrex FRP fabrication capabilities
As fiberglass fabricators, we specialize in producing equipment such as fiberglass reinforced plastic pipe, fittings, tanks, scrubbers, elbows, and reducers. We also manufacture flat panels for external coverings over insulated tanks, as well as internal shelves and baffles for scrubbers and tanks. The molding flexibility of fiberglass enables us to custom fabricate flanges in various sizes, along with many other smaller components and fiberglass reinforced plastic products.
- FRP piping systems and fittings (flanges, reducers, elbows)
- FRP scrubbers
- FRP tanks
- Custom FRP fabrication (specialty items: strainer baskets, trays, other types of tanks (square), hoods, acid baths, anode boxes)
- FRP linings (steel, concrete, FRP)
- FRP inspections, testing and field services
Why Abtrex?
- AWS & ASME Qualified
- 5 Decades of Growth and Experience
- Turnkey Abilities
- Proven Project Management Skills
- Numerous Strategically Located Bases of Operation
- 24 Hour Emergency Response
- Commitment to Continual Improvement