Corrosion protection is vital for preserving the integrity of metal structures by preventing the gradual deterioration caused by environmental factors and corrosive chemicals. Effective corrosion resistance measures not only extend the lifespan of materials but also contribute to maintaining structural stability and safety. Equally crucial is wear resistance, ensuring durability against friction and abrasion, minimizing the impact of mechanical stress and preserving the functionality of components over time. To fulfill its intended function, the rubber lining or coating must maintain its integrity, guaranteeing that any substance it comes into contact with does not penetrate it and cause corrosion to the underlying substrate.
Have you ever wondered how we inspect the integrity and ensure there are no holes or voids in the rubber lining or paint coating? One method is called holiday detection. It is a technique used to identify defects in the protective coatings and linings applied to metal surfaces. Many of these defects are difficult to visually see, hence the necessity for mechanical means like a holiday detector. Holiday detection testing can be categorized into two groups: low-voltage testing and high-voltage testing.
Both groups involve applying an electrical voltage to the coated or lined surface and using a probe or electrode to detect any electrical current flow or spark indicating the presence of a defect or a holiday in the liner. The choice between low-voltage and high-voltage testing depends on the thickness of the lining or coating and the specific requirements of the inspection.
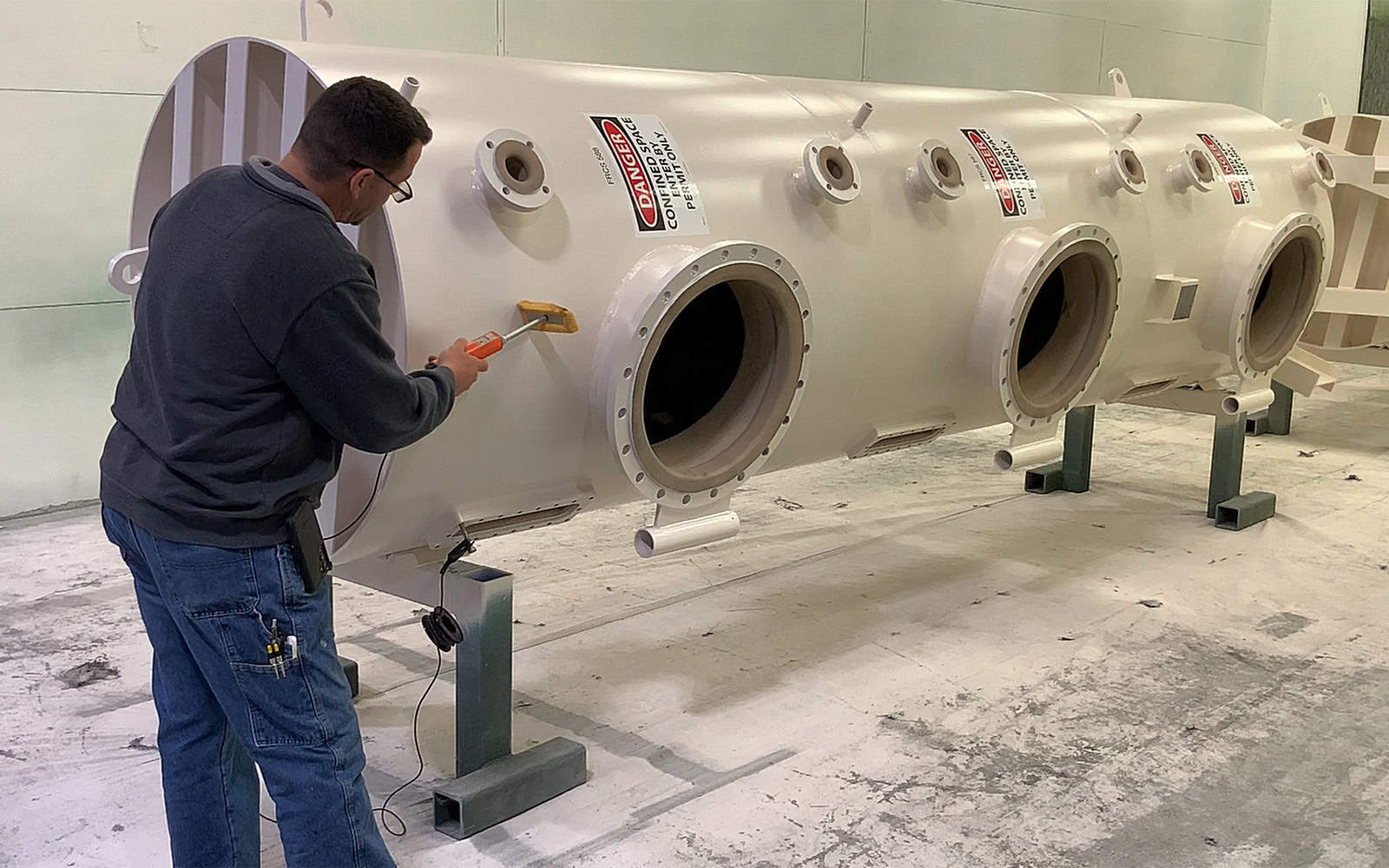
Holiday Inspection of a Tank Coating Using a Sponge Tester
Low-voltage testing
Low-voltage testing is a holiday detection method employed to inspect protective coatings thinner than 500 microns or 20 mils. This method typically uses a voltage of 9 volts for testing coatings under 12 mils in thickness and a voltage higher than 9V for those with a layer from 12 to 20 mils. Thinner coatings require a lower voltage because they have a lower dielectric breakdown voltage, an electric potential at which an insulating material becomes conductive. If the voltage is too high for a thin coating, it may lead to premature dielectric breakdown, causing the coating to become conductive even in areas without defects, which can result in false readings.
At Abtrex, we use a low-voltage detection testing procedure to inspect the proper coverage of paint and to make sure that there are no pinholes or leaks in the lining. This procedure involves using a detector with a damp cellulose sponge attached to one end of the tester with a metal clamp on the opposite end, used as an electrical ground. Ensuring the sponge lies flat on the surface, the inspection is carried out by moving it at a moderate speed over the coated surface. If there is a defect or a holiday in the paint coating, the moisture in the sponge will facilitate the flow of electrical current to the steel substrate, enabling the detection of the flaw. The detector signals the identification of a defect with a sound alarm. All identified holidays are then repaired by grinding or abrading the area, and applying new layers of the specified coating. Once the repair is completed and the coating dries, the testing procedure is repeated to ensure the area is defect-free.
Holiday Sponge Test Video
High-voltage testing
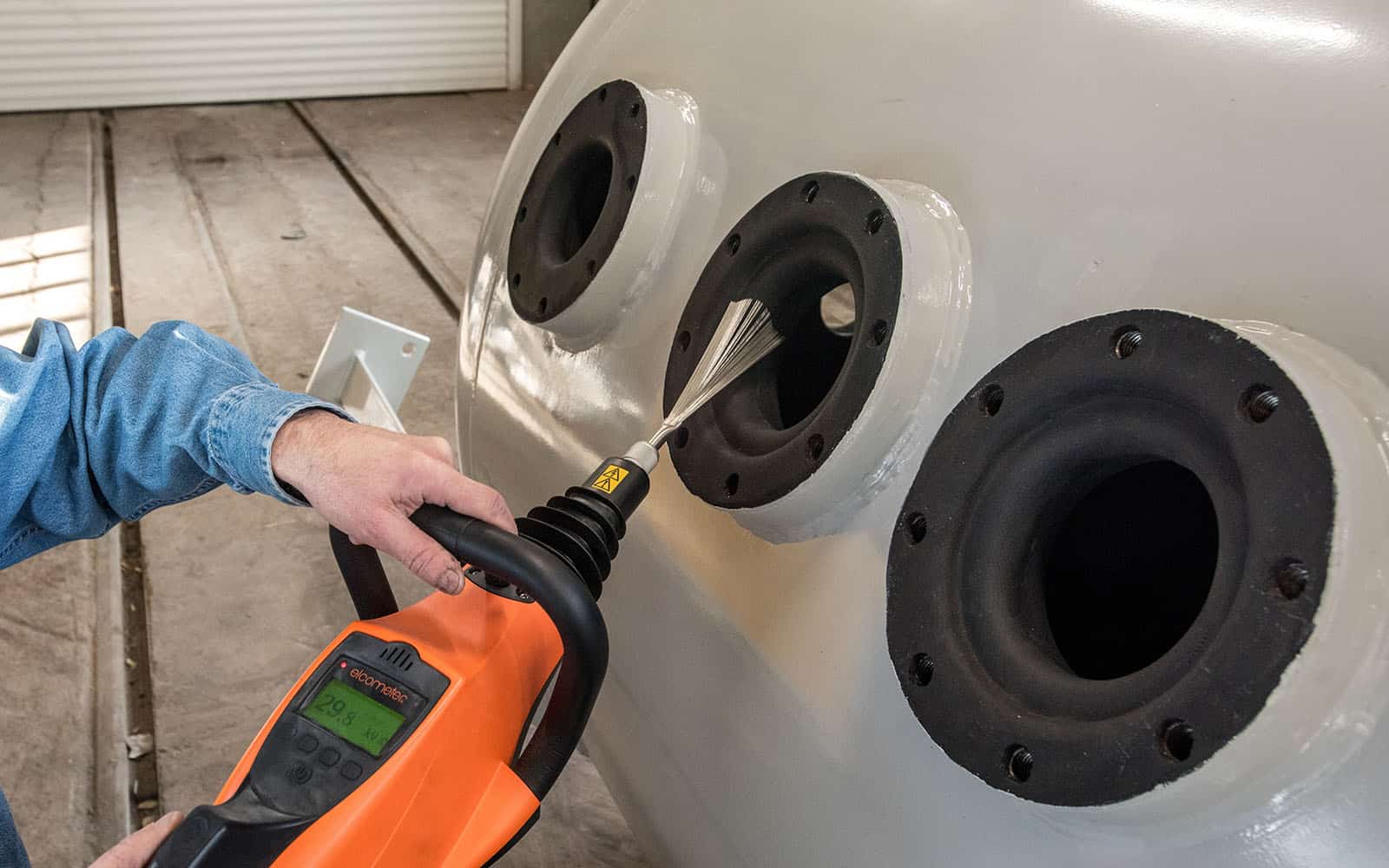
Holiday Inspection of a Rubber Lined Tank Using a Brush Wand Spark Tester
This quality inspection is conducted with a use of a high-voltage device called spark tester. The purpose of a high-voltage tester is to detect pinholes, leaks or voids in rubber linings and coatings thicker than 500 microns, or 20 mils. This spark testing technique requires use of a higher electric potential device, because the dielectric breakdown voltage increases with the thickness of the lining material. Use of a high-voltage detector will ensure an electrical current will effectively pass through the thicker lining, making it possible to identify any potential flaws.
Our quality technicians use a high-voltage tester to effectively detect and locate any pinholes or leaks in the rubber linings. This inspection procedure requires the use of a probe attached to the detector. Like the low-voltage testing procedure, the test is conducted by moving the probe over the rubber-lined area continuously. If a leak is found, the device will discharge a visible white spark from the probe to the metal surface through the air path, indicating the presence and location of a holiday in the lining. Any detected leak will then be repaired by grinding the defected area and applying a lining patch as necessary. When the rubber repair is completed, the testing process is repeated to confirm that the area is free of pinholes and holidays.
Spark Test Video
Ensuring the integrity of protective coatings and linings of industrial assets through comprehensive holiday testing is paramount for longevity and safety.
At Abtrex, we specialize in corrosion and abrasion resistance. If you are seeking expert solutions for rubber linings or coatings inspection, don’t hesitate to reach out. Contact us to discuss your specific needs and discover how our services can enhance the performance and durability of your industrial infrastructure.