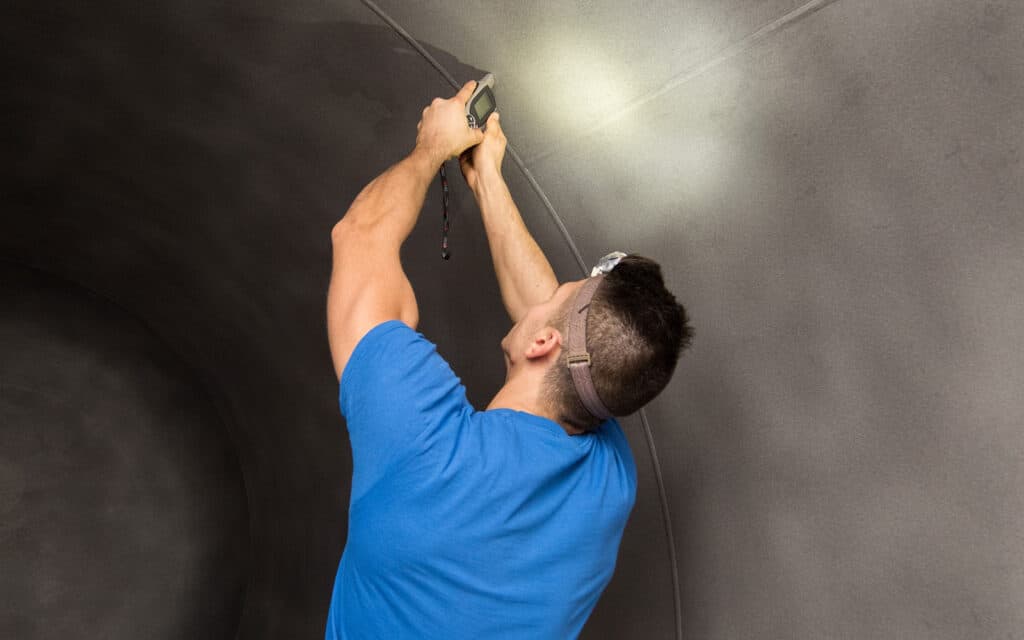
Why Surface Profile Testing Is Critical for Proper Adhesion of Rubber Linings
Surface preparation is essential to promote strong mechanical and chemical bonding between the substrate and rubber lining. It is the most fundamental step in the lining process, ensuring that the corrosion protection system performs effectively. The lining material, whether natural rubber or a synthetic blend, must meet standards for thickness and hardness. However, rubber lining systems, even when specified correctly for the service environment, won’t perform well without proper surface preparation.
An improperly prepared metal surface is one of the leading causes of corrosion barrier failure. If the specified surface profile and cleanliness level are not achieved the lining may not adhere properly. Simply put, improper surface preparation can shorten the service life of the lining and reduce its corrosion protection capabilities.
At Abtrex Industries, every rubber lining application begins with cleaning, blasting and/or mechanical scarification process, followed by inspection of the surface profile. This ensures each project meets our strict internal standards and industry best practices.
Surface Profile Testing Methods
Surface profile is quantified by measuring the depth of the valleys in relationship to the top of the peaks. It tests the roughness and texture of a substrate after abrasive blasting by measuring the distance between the highest peaks and the lowest valleys. The ‘anchor’ profile ensures the lining material adheres to the substrate.
One of the most widely recognized industrial standards, ASTM D4417-20 ‘Standard Test Methods for Field Measurement of Surface Profile of Blast Cleaned Steel’ outlines four methods to measure surface profile:
- Method A – Visual Comparator – Compares the blasted surface to pre-made reference plates with known roughness values
- Method B – Depth Micrometer – Uses a fine conical probe to measure the distance from peaks to valleys
- Method C – Replica Tape – Involves pressing a special foam replica tape against the substrate to create a reversed image of a surface, which is then measured with micrometer
- Method D – Electronic Profilometer – Uses electronic instrument to scan the surface and generate a digital profile of its texture
Surface Preparation and Testing Process
Before the metal substrate can be examined the surface must be thoroughly cleaned, free from dust or blast media debris. Once cleaned, locations for representative samples must be selected. The SSPC-PA 17-2020 ‘Procedure for Determining Conformance to Steel Profile/Surface Roughness/Peak Count Requirements’ specifies identifying three 6×6 inch areas for each blast unit used per work shift.
Depth Micrometer Profile Testing
Before using the depth micrometer, the instrument must be zeroed out on a glass zero plate and verified on a metal shim to ensure accuracy. During testing, the gauge is placed perpendicularly on the blasted surface and slightly pushed downwards, allowing the conical probe to measure the distance between the surface peaks and valleys. The result is displayed on a digital screen of the measurement instrument.
Per D4417-20, there are (3) acceptable parameters for measurement quantities:
- Measure at a sufficient number of locations to characterize the substrate as specified or how many readings are agreed upon between the parties involved.
- For each selected area, ten readings must be taken. Record the maximum values from each location, then determine the average from all locations.
- Take ten readings at each location and average those readings. Then determine the average from all three locations.
It must be noted that ‘outliers’ will occur when taking digital depth micrometer readings. You simply ‘toss’ those readings and replace them with measurements that are considered to be in the specified range.
Replica Tape Surface Profile Testing
The replica tape method involves pressing the Testex tape onto the cleaned, blasted surface. The tape consists of a compressible foam layer bonded to a 2-mil mylar film. When pressed against a roughened steel substrate, the foam collapses and forms an reverse impression of the surface profile.
Depending on the expected roughness, one of four tape grades is selected to ensure accurate measurement:
- Coarse Minus – 0.5-0.8 mils
- Coarse – 0.8-2.5 mils
- X-Coarse – 1.5-4.5 mils
- X-Coarse Plus – 4.0-5.0 mils
After the appropriate tape is chosen, a section is cut from the roll and applied to the cleaned, blasted surface with the foam side facing down. Next, the tape is burnished with the rounded tip of a plastic or metal stick. This action allows the foam to penetrate the valleys of the texture and create a reverse image of the surface profile. When the backing turns a uniform gray, it indicates that the profile is replicated. At that point, the tape can be removed and inserted into a spring-loaded micrometer.
To account for the Mylar backing of the replica tape, it is standard practice to adjust the gage reading by subtracting 2 mils. A common practice is to ‘dial back’ the gage to ‘8’. For accuracy, at least two readings should be taken at each location.
One of the key benefits of this method is that the replica tape serves as a durable, long-term archival record of the surface condition, making it ideal for future reference and quality documentation.
Surface profile testing is a critical step in securing strong adhesion and reliable performance of rubber linings. At Abtrex, we utilize precise measurement methods—including depth micrometers and replica tape—to ensure that every substrate is prepared to the highest standard. This not only enhances mechanical bonding but also protects the integrity of the lining system over time.
By adhering to industry standards such as ASTM D4417 and SSPC-PA 17, Abtrex delivers rubber lining solutions that stand up to the toughest industrial environments and provide lasting corrosion protection.
Contact us to discuss your project needs and discover how we ensure your equipment is built and protected to the highest standards against chemical and abrasion damage.